Food Safety Audit Innovations
Expanded on-site and virtual options to meet the Covid-19 challenge and beyond
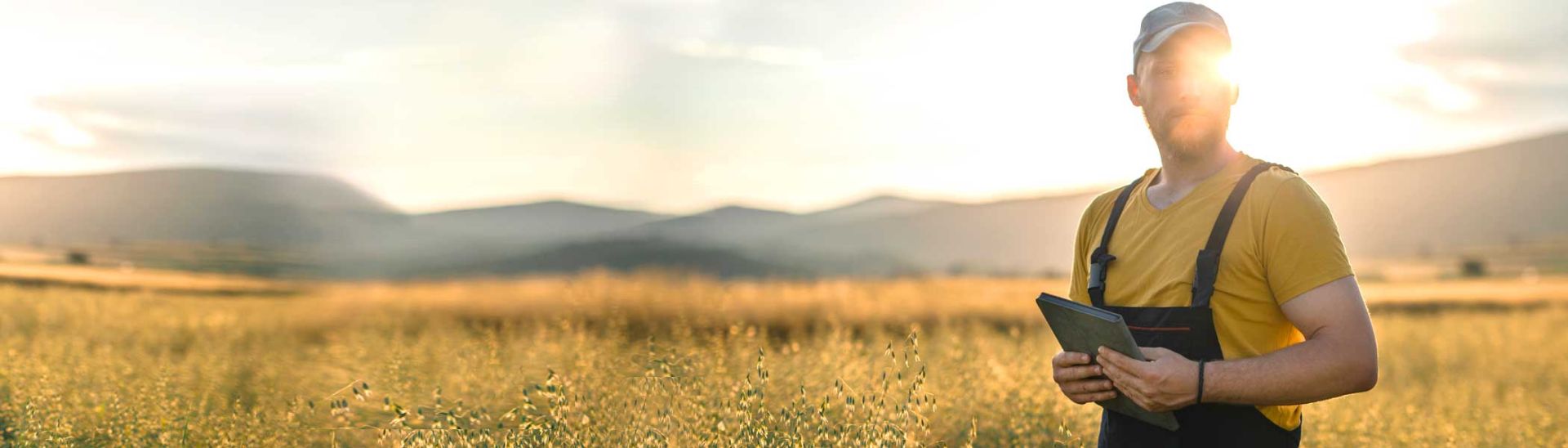
What is Food Safety Audit Innovations?
Food workers stand at the frontlines of the Covid-19 global pandemic, ensuring that we continue to be able to eat fresh and healthy food, despite unprecedented challenges. Companies like yours face production schedule disruptions, supply chain interruptions, volatile swings in demand, and potential worker shortages. Amidst these changes, there has never been a more urgent need for sound food safety practices backed up by independent audits. In response, SCS has developed diverse on-site and remote food safety auditing options to help you keep your food safety program on-track.
Why choose SCS?
Since 1984, SCS Global Services has been a leading pioneer in science-based food safety auditing and certification. Our enhanced auditing protocols and innovative technologies are comprehensive and non-intrusive.
These approaches combine state-of-the-art, virtual video livestream and recording technologies with more than three decades of in-depth auditing expertise, to help you assure GMP or GFSI level performance. Our auditing solutions can also enhance the audit experience for our clients, now and into the future.
Eligibility
Eligible Companies
Any food processing, packing, or storage operation interested in enrolling in or already enrolled in a recognized food safety audit and certification program may take advantage of these services, whether previously audited by SCS or another third-party.
We can also audit the vendors in your supply chain, verify audits conducted by others, conduct pre-assessment audits, and conduct gap assessments for companies advancing toward more complex certification options. SCS is here for you.
- Types of Audits
- Benefits
- FAQs
- Process
Types of Food Safety Audits
Audits are tailored to meet company needs, taking into consideration applicable travel restrictions, access restrictions, and safe social distancing. Our new on-site virtually enhanced audits and remotely conducted virtually enhanced audits are available when traditional on-site audits are not an option:
- NEW: On-Site Virtually-Enabled Audits
Auditors conduct live virtual “walk-through” inspections, providing moment-by-moment instruction to the appointed on-site food safety staff counterpart, using video livestream technology, high-resolution 360° video cameras, GPS, and other tools. Having auditors physically on-site supports optimal livestream connectivity, on-the-spot camera footage review, the opportunity for face-to-face employee interviews, and other benefits. Applicable when permitted on the premises but restricted in terms of full access. - NEW: Remote Virtually-Enabled Audits
These audits utilize all of the tools of the on-site virtually-enabled audits – video livestream technology, high-resolution 360° video cameras, GPS, and more – directed by auditors from a remote location. They also include remote employee livestream or phone interviews, surveys and a text messaging hotline. Applicable when auditors have no on-site access at all. - Full On-Site Audits
Auditors follow standard audit protocols, including site inspections, confidential face-to-face employee interviews, documentation reviews[lb2] , and more. Auditors carry travel certificates, use PPE, and follow strict social distancing guidelines. Applicable when normal travel and site access are permitted, and auditor safety is assured. - Desk Audits
Desk audits are typically conducted as a preliminary step in the audit process, or as a means to shorten subsequent virtual or on-site audits. Desk audits may also be conducted when off-site documentation reviews and remote interviews are sufficient to meet program needs. Applicable as a preliminary step or when desktop reviews alone are required.
Our new, virtually-enabled on-site and remote audits provide comparable, credible assessments and results in this time of reduced site accessibility. Benefits include:
Addressing all aspects covered by traditional 1-day (e.g., GMP-level) and 2-day (e.g., GFSI-[lb1] level) on-site audits, including administrative/policy conformance, identification and review of corrective actions, security and employee safety for a complete audit
- Utilizing high-resolution 360° spherical recorded camera technology capable of both continuous video and stop-action, frame-by-frame review, as well as livestream video communications and remote video monitoring
- Allowing time-stamping of audit, as well as GPS coordinates, for validation
- Optimizing livestream connectivity when on-site due to proximity (e.g., via wifi booster)
- Working closely with your food safety staff on-site, our auditor can tap their expertise in real time and reinforce their inhouse role in driving food safety performance and improvements
- Allowing for same-day review of camera footage (video and still images) by the auditor on the spot
- Enabling face-to-face, confidential interviews with employees while maintaining a safe physical distance
Moreover, these audit approaches provide some unique enhanced benefits beyond traditional on-site inspections, allowing our auditors to:
- “Play back” specific footage several times to focus more closely on details (not possible during a normal inspection)
- Request additional video, photos or data as needed on the spot
- Visually point out to your food safety staff specific issues of interest, captured on camera for their review
Some companies are already recognizing that these innovations provide benefits that have implications beyond the current COVID-19 challenge, not only enhancing the audit process, but directly supporting and reinforcing the objectives of the company’s food safety team.
How does an on-site virtually-enabled audit compare to a traditional on-site audit?
During the on-site virtually-enabled audit, the SCS auditor provides a 360° spherical camera to a designated company food safety staff representative, and establishes a livestream video communications link (e.g. Facetime), in order to direct the representative in a detailed walk-through inspection in real time. The camera records continuous video in all directions, as well as stop-action, frame-by-frame images and GPS coordinates, all of which is then reviewed by the auditor on-site.
How does an on-site virtually-enabled audit compare to a remote virtually-enabled audit?
During the on-site virtually-enabled audit, the SCS auditor and company staff representative enjoy optimum livestream connectivity, supporting real-time direction and communications. Once the audit is completed, recorded camera images can be reviewed on the spot, and can be supplemented as needed. When the audit is conducted from a remote location, the camera must be shipped to the auditor for review.
How do you ensure confidentiality when conducting staff interviews during virtually-enabled audits?
Confidentiality for staff interviews is ensured in several ways. While on-site, the auditor and employee can have live, face-to-face interviews at a safe distance. Virtual audits conducted via livestream can confirm that employees are alone when being interviewed. Text hotlines and other tools can further support the interview process.
How do you ensure that your inspection is complete when conducting virtually-enabled audits?
Proper preparation is integral to ensuring that the inspection will be completed properly. This will typically involve review of documents and records, as well as a site floorplan and process flow information. The virtual audit is carefully planned out in advance to ensure that all essential points of interest are evaluated, and employee interviews and follow-up procedures complete the process.
Are virtually-enabled audits recognized as substitutes for traditional on-site audits?
As virtual technologies and protocols come into in increasing use, their many applications are being carefully studied and benchmarked to determine and ensure their equivalence to standard auditing protocols. While they are not currently accorded formal equivalence status, these technologies are rapidly emerging as viable options that could ultimately change the face of food safety auditing in the future. For now, these audits serve well as interim assessments, particularly as workforce safety procedures, production volumes, and other variables are in flux, as well as pre-assessments.
Virtually-enabled on-site and remote food safety audits are intended to simulate the full on-site experience. The steps for conducting these audits will vary depending on the specific level of audit to which you aspire. In general, however, the process can be summed up as follows:
- Apply for Auditing
Fill out an SCS Application form, which provides us with the details of your site and operation. Contact SCS at [email protected] to request guidance. SCS staff returns a proposal to you for signature. To initiate the certification process, return a signed proposal and Work Order - Complete Questionnaire
Provide documentation and information related to SOPs, policies, floorplans, employee rosters, etc. for the auditor’s use in preparing for the site inspection. - Desk Audit
The auditor conducts a documentation review for completeness. Some audit schemes require a formal desk review, including an issuance of findings that should be addressed before the on-site portion of the audit is conducted. - Schedule the Site Inspection
SCS assigns an auditor and audit dates are proposed. Once confirmed, an audit plan is provided to ensure that your team is prepared. - Conduct Virtually Enabled Inspection
A site audit is carried out to ensure that your operation is in compliance. A company food safety staff representative will be selected to carry the virtual recording and livestream equipment, at the direction of the SCS auditor, in accordance with the audit plan. Detailed protocols vary depending on whether the inspection is managed on-site or remotely by SCS. Depending on the audit scheme, a team meeting may be required at the beginning and the end of the audit. At the conclusion of the inspection, the auditor will explain the audit results, including any non-conformities. - Audit Report Review
The auditor prepares and submits an audit report. Identified non-conformities must be addressed and evidence of correction provided to SCS within a specified timeframe. The auditor reviews and closes out non-conformities as required. Once this process is complete, the auditors submit an audit report. - Issue Audit Score
SCS conducts a final technical review of the audit report and Corrective Action documentation and issues the final audit score. Final audit results are sent to you and posted, and are sent to specific retailers as requested. For audit schemes leading to certification, a final certification decision is made. If certification is granted, SCS issues the certificate and final report to the facility/operation and posts its reports and certificates to online databases when requested by buyers.
Request Information
Ready to get started or need more info? Connect with us.